Air Gaging LLC finished a project with a Tier Automotive supplier for an automated measuring station for an engine component. The automated air gaging cell is in an enclosed cage and is part of the closed loop manufacturing process. Parts are placed into the cell as blanks and are then sent through two Fanuc Robodrill machines. They are then blown off to remove chips and coolant. There is a Fanuc LR200i robot that is placing the parts unto the air gaging stations. We are using a Stotz MRA measuring computer with Ethernet and Profibus communications. The Siemens controller sends the Stotz gage the serial number that is read from a data matrix engraved on the part. We then record this serial number so that all of the measurements that are taken are stored with that serial number. There are 6 measuring stations. Five of the stations are measuring diameters with tolerance from +/-0.007 mm upto +/-0.012 mm. One of the stations is measuring perpendicularity using 4 circuits of cross channeled air and then calculating the perpendicularity based on the four individual readings. After each station, we report to the PLC a pass/fail signal. The logic is built in that if 3 parts in a row fail for the same measurement, it will stop the system. A monitor is placed on the outside of the cage so the operator can monitor all measurements and SPC in real time. The system is also using part like masters so the calibration of the gaging system is also handled automatically with the robot. The measurement cycle is 45 seconds per part. Once the part has finished in the automated measuring station, it is sent through a parts washer. The part is oiled and placed into shipping containers all without a single human hand touching the part.
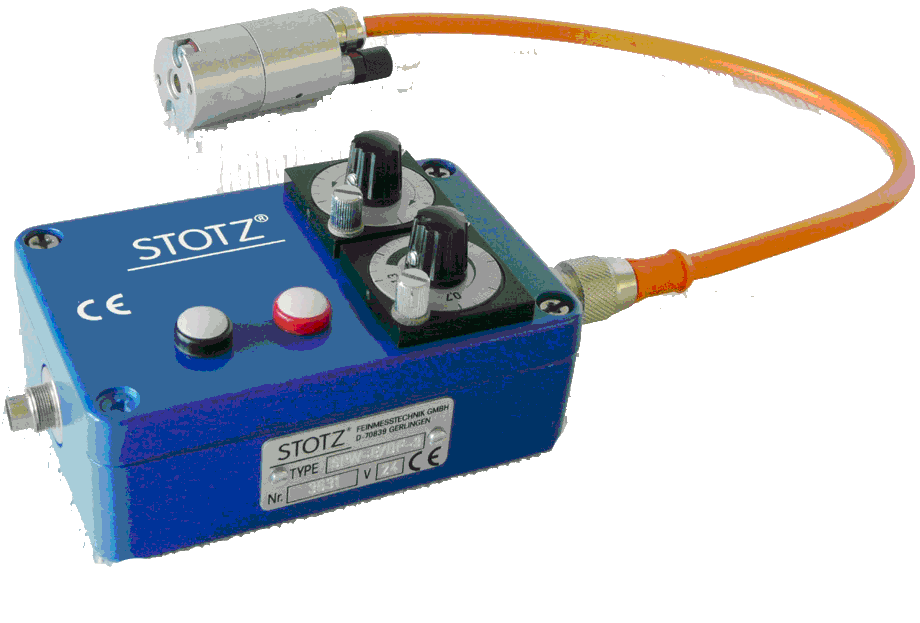